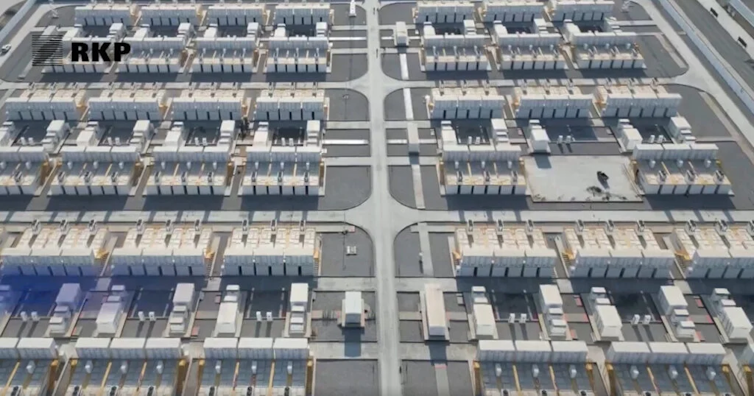
As more and more solar and wind energy enters Austalia’s grid, we will need ways to store it for later. We can store electricity in several different ways, from pumped hydroelectric systems to large lithium-ion battery systems. We can also use flow batteries.
These are a lesser-known cross between a conventional battery and a fuel cell. Flow batteries can feed energy back to the grid for up to 12 hours – much longer than lithium-ion batteries which only last four to six hours. I was one of the inventors of one of the main types of flow battery in the 1980s.
It has taken decades to bring batteries like these to commercial viability. But they are, finally, arriving in earnest. This year, the Australian government launched a national battery strategy to expand domestic manufacturing of batteries.
This A$500 million strategy will focus on the well-known lithium-ion batteries which power phones and cars. But it will also include flow batteries. Batteries are becoming more and more important.
They can now power cars, houses and even cities. Huge amounts are being spent on commercialising new battery chemistries to electrify transport and make it possible to green the power grid. To date, most of Australia’s grid-scale batteries use chemistries such as lithium-ion.
But as our grid shifts to renewables, we’ll need longer duration storage to eliminate the need for fossil fuel backup generators. That’s a task well suited to flow batteries. What makes flow batteries different? Conventional batteries such as lithium-ion batteries store power in their electrodes, commonly a metal.
Flow batteries store power in their liquid electrolytes. Electrolyte solutions are stored in external tanks and pumped through a reactor where chemical reactions take place at inert electrodes to produce energy. Flow batteries can be altered to suit requirements of a task.
You can change how much power you generate (in kilowatts) and how much storage (in kilowatt-hours). If you want more storage, you increase the volume of electrolytes in the tanks. As you increase storage capacity, the cost per kWh of stored energy decreases dramatically.
This is because you only have to add more liquid electrolytes rather than adding entirely new battery packs, as in conventional batteries. This means flow batteries are currently the cheapest way to store electricity for longer durations (over 8 hours). Unlike lithium-ion batteries, flow batteries can run for tens of thousands of cycles and the electrolyte can last much longer – or even indefinitely.
One downside is their weight – these batteries are very heavy and are not portable. To date, zinc bromine and vanadium redox batteries have undergone the most testing and commercial implementation. Vanadium flow In the mid-1980s, my colleagues and I pioneered vanadium redox flow batteries at the University of New South Wales.
Vanadium is an unusual metal. It can exist in different states of oxidation in the same solution. That means you can run a battery using just one element, instead of two, as in other chemistries.
Doing so lets you avoid cross-contamination and gives the electrolyte solution an indefinite life. After decades of development, vanadium flow batteries are now being commercially produced by companies in Japan, China and Europe, with several gigawatt hours worth of capacity now installed globally. China, the world’s largest vanadium producer, has recently approved many large new vanadium flow battery projects.
In December, the world’s largest came online in Dalian, China, with 175MW capacity and 700 mWH of storage. Australia’s first megawatt-scale vanadium flow battery was installed in South Australia in 2023. The project uses grid scale battery storage to store power from a solar farm.
The main challenge to commercialisation has been securing vanadium, which has fluctuated wildly in price and supply due to competing demand from the steel industry . This is likely to change. Government investment in critical minerals has fast-tracked several new vanadium mines and processing plants.
Australia could become a major global vanadium producer in the future. In 2023, Townsville became home to Australia’s first factory producing vanadium electrolyte. Iron and zinc Flow batteries can be built from many different chemistries.
Two other promising chemistries are iron-iron and zinc bromide. Iron flow batteries have been under development in the United States since 2011. These cells use iron, salt and water, avoiding the need for vanadium.
In Australia, Queensland-based company ESI Asia Pacific is planning to develop their own iron flow batteries at a new factory in Maryborough once construction is complete in 2026. While iron is plentiful and cheap, these batteries rely on high purity iron chloride to reduce iron corrosion. This may mean electrolytes cost significantly more than expected.
Field testing data is limited to date. Zinc bromine batteries use a solution of zinc, a metal, and bromine, an element extracted from salt water. The chemistry means each cell has a higher electricity output than other flow batteries, but it comes with a challenge – finding ways to stop the growth of tree-like dendrites inside the cell, which can disrupt energy production or trigger short-circuits.
Battery-powered future? Creating a larger Australian battery industry will take time and funding. But the demand for batteries will skyrocket globally in coming years, across the electricity and transport sectors. As we work to electrify road transport, we will see demand for electricity increase as well as demand for the lithium-ion batteries now ubiquitous in electric vehicles.
As a major producer of lithium, Australia could also manufacture lithium batteries too, for domestic use or export. To compete globally, we would need to embrace automation. Despite different chemistries, flow batteries share many common components which could be made locally and boost energy self-sufficiency.
Flow batteries have long required time consuming and expensive manual assembly. But it’s now possible to automate assembly lines, which will cut costs and make Australian-made batteries better able to compete. My colleagues and I are working on this challenge at present.
Within a decade, Australia could become a globally competitive battery maker and exporter of critical minerals. Doing so would help the shift to clean energy, both domestically and around the world..